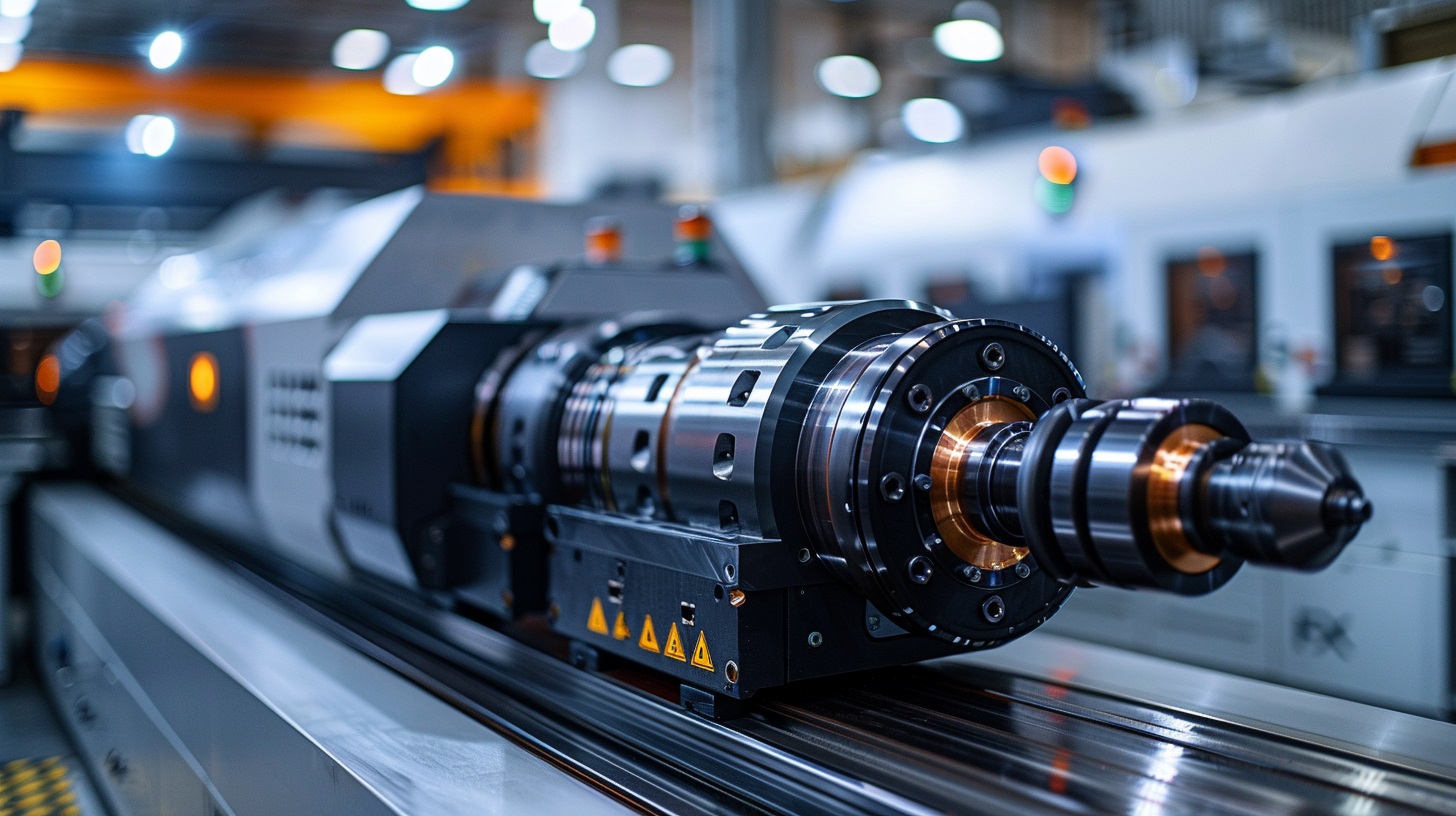
As the metal cutting manufacturing industry expands and progresses, effective risk management becomes increasingly crucial. It is a fundamental component of any business strategy, especially in this sector, where poorly managed risks can result in substantial financial setbacks, damage to reputation, and safety issues impacting both employees and clients.
Keeping abreast of palladium market news and analysis is vital, as it offers insights into industry trends, aids in anticipating potential risks, and supports well-informed decision-making.
Spotting potential threats
The first step in solid risk management is spotting potential threats. Common risks in metal cutting manufacturing include equipment failures, workplace accidents, supply chain hiccups, and changing market conditions. For instance, if a machine suddenly breaks down, it can stop production and lead to missed deadlines and financial penalties.
Once these risks are spotted, it’s crucial to assess their potential impact and likelihood. This thorough assessment lays the groundwork for developing strategies to tackle these risks effectively.
Rolling out safety programs
Implementing a solid safety program is one of the best ways to manage risks. These programs should cover regular safety training for employees, highlighting the importance of personal protective gear and emergency procedures.
Routine equipment checks ensure everything is running correctly and safely. Tailored safety protocols and procedures can prevent accidents and injuries. Clear communication channels are also key, letting employees easily report any safety concerns or hazards. This open dialogue encourages a culture of safety and awareness within the organization.
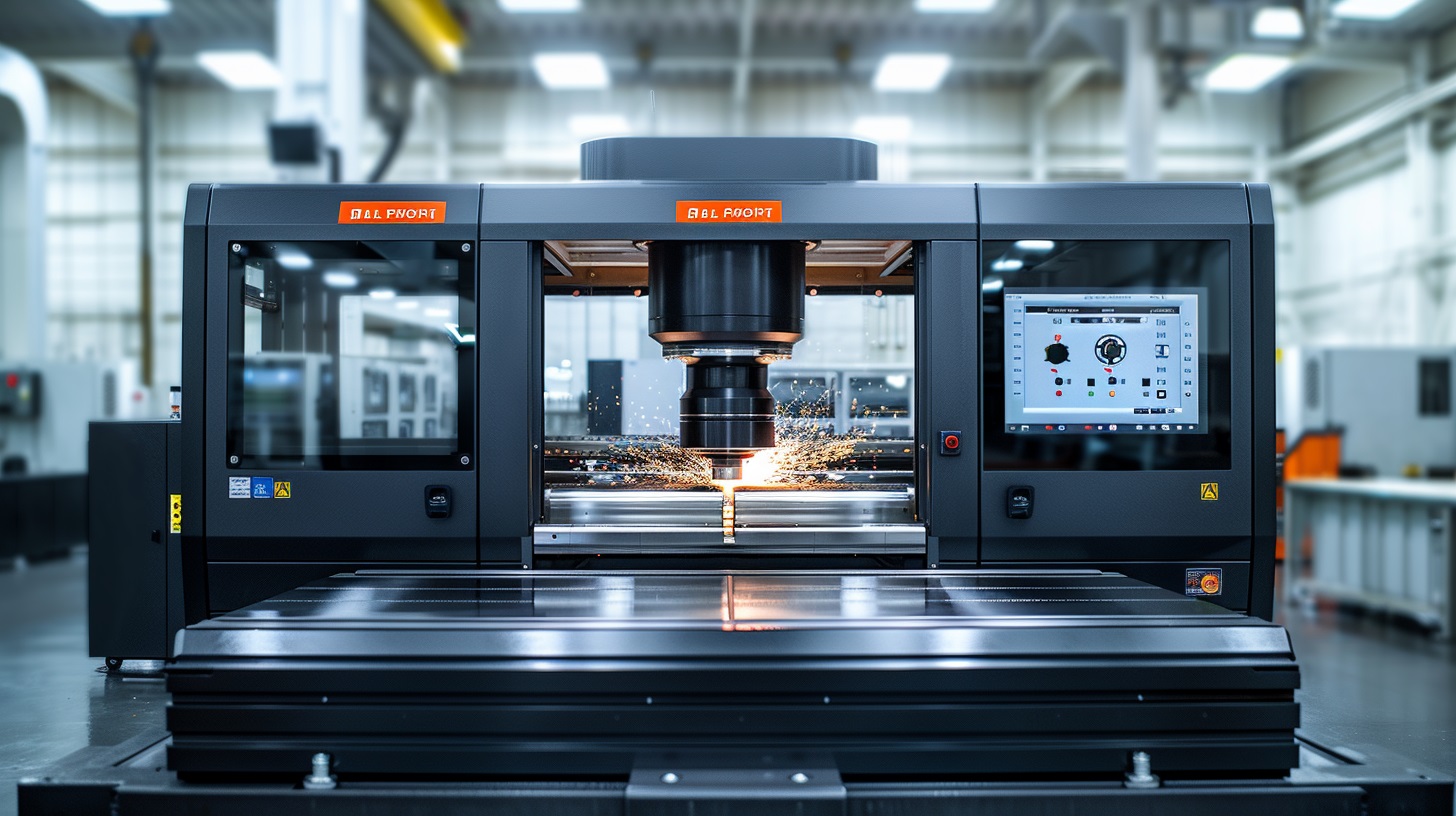
Setting up contingency plans
Another vital part of risk management is setting up contingency plans. These plans should outline the steps to take during a risk event, specifying roles, responsibilities, and needed resources. For example, if a supply chain issue arises, a contingency plan might include sourcing materials from alternative suppliers.
Regularly reviewing and updating these plans is necessary to keep them relevant and effective. This proactive approach minimizes downtime and ensures business continuity during unexpected events.
Investing in risk management tools
Beyond safety programs and contingency plans, companies should think about investing in risk management tools and technologies. Predictive maintenance technology, for example, can prevent equipment failures by analyzing performance data and scheduling maintenance before issues pop up, reducing downtime and lost productivity.
Supply chain monitoring tools can help anticipate and mitigate potential disruptions by providing real-time insights into supplier performance, allowing for quick adjustments to procurement strategies if needed.
Regular evaluation and tweaking
Lastly, it’s important to regularly evaluate risk management strategies to ensure they’re working well. This could involve conducting risk assessments to spot new or changing threats, reviewing incident reports to learn from past experiences, and gathering feedback from employees and stakeholders. With this info, companies can tweak their strategies and make necessary adjustments, keeping them in line with industry standards and best practices.
Wrapping up
In wrapping up, effective risk management is crucial for companies in the metal cutting manufacturing industry. By spotting potential risks, rolling out solid safety programs and contingency plans, investing in risk management tools and technologies, and continually reviewing and tweaking strategies, companies can minimize their exposure to risks and stay competitive in this fast-changing industry.
This proactive approach not only protects the company’s assets but also supports sustainable growth and success.